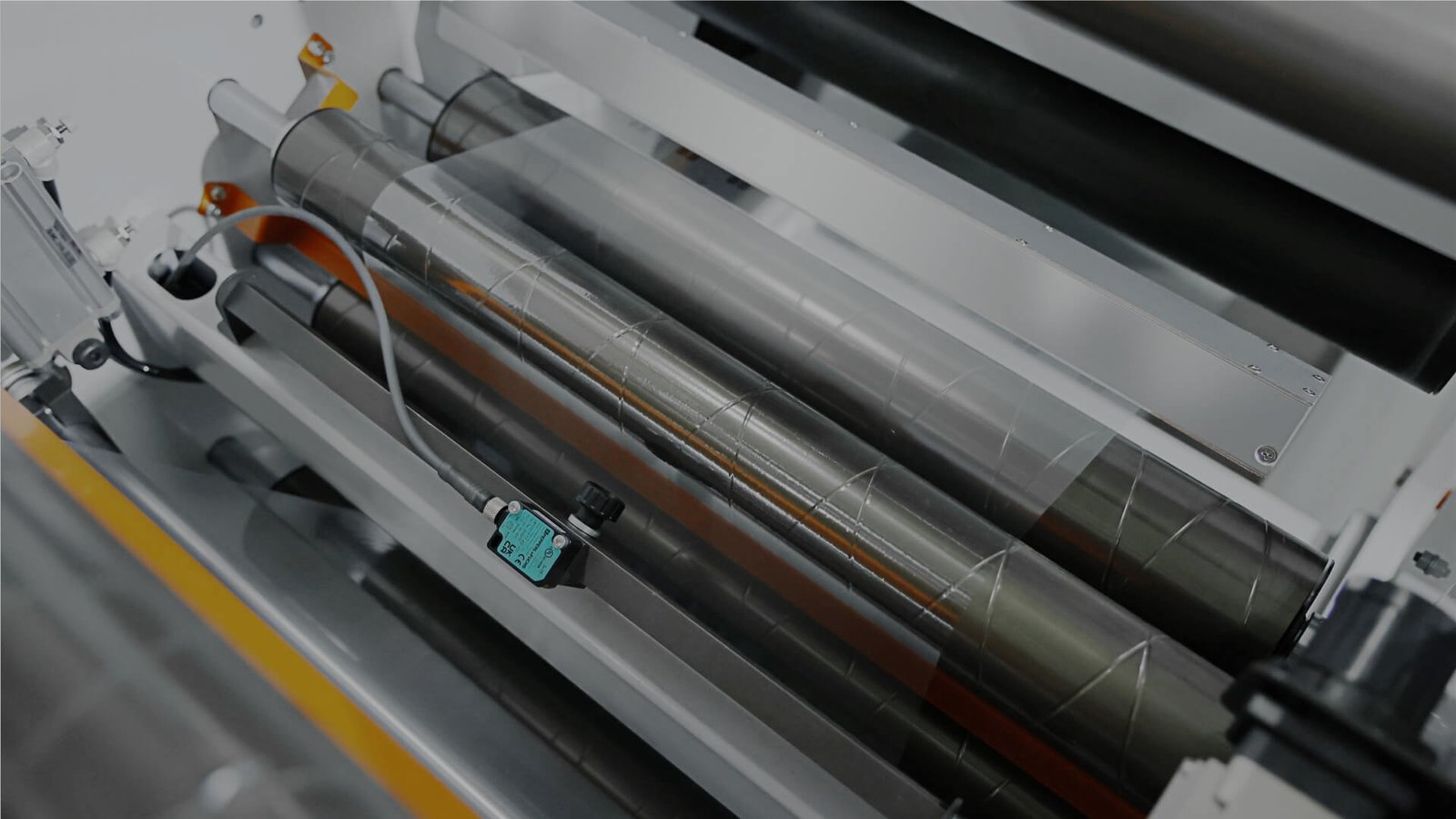
Combination of IUV modular technology and digital control technology.
Automatically sense the position and width of the printing material, and automatically control the working area of the entire LED UV curing system.
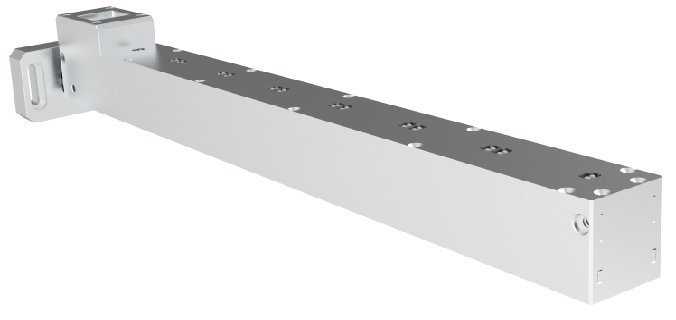
Specification

Installation Location: | After correction, before the first print unit. |
Light Segment Control Precision: | 10mm, 36mm, 53mm |
Sensor and Material Distance: | 1-3mm |
Expected Extra Energy Savings: | 30% up |
Working Environment: | -10~35℃ |
The automatic sensing system monitors the position and width of printing material in real-time.
Intelligently adjusting the UV LED curing area and power for optimal curing performance across different inks, while maximizing energy efficiency.
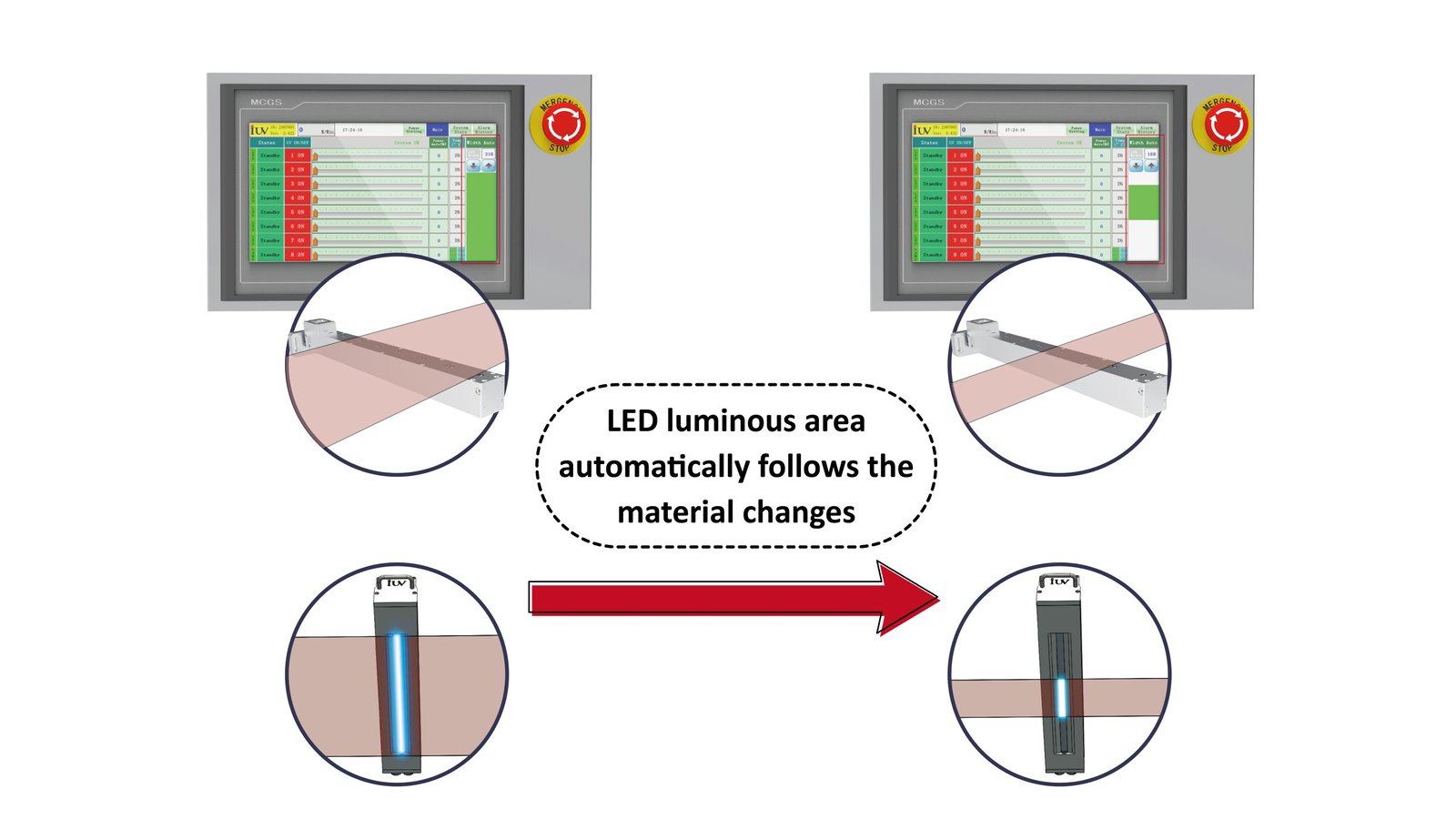
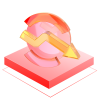
Automatically sensing material changes, curing only the areas covered by the material, reducing unnecessary energy consumption.
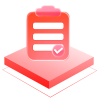
Printing Quality
Precise curing area control, ensures consistent print quality and reduces quality issues caused by uneven curing.
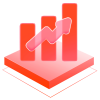
Efficiency
Adjust the curing area in real time,eliminating the need for manual intervention and adjustments, boosts production efficiency.
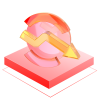
Temperature
Minimize unnecessary UV energy, reduce material temperature, maintain consistent printing quality and minimize material loss or non-conforming products.
By integrating automatic sensing technology into your printing equipment, significant energy savings can be achieved.
For instance, with a 360mm printing width, six-color printing setup, and an average operational schedule of 10 hours per day over 22 days each month, the energy consumption varies notably between traditional mercury lamps and LED UV systems.
Traditional Mercury Lamps: High energy consumption due to continuous operation and heat generation.
LED UV Systems with Automatic Sensing: Reduced energy usage by adjusting the curing area to match the material width, ensuring efficient power usage.
Implementing LED UV systems equipped with Automatic Sensing Technology can lead to substantial energy savings, enhancing both operational efficiency and cost-effectiveness.
The transformative journey of the Omet Xflex X6 Flexo Press with IUV LED UV curing system.
Nilpeter
With IUV’s LED UV curing system, enhanced production capabilities, and sustainability.
OMET
The project’s success with IUV ability to enhance print quality, increase productivity, and sustainability.
Bobst
With IUV’s LED UV curing system, enhanced production capabilities, and sustainability.
Gallus
IUV's LED UV retrofit for fast curing , energy savings, and extended equipment lifespan.
Mark Andy
The UV LED upgrade for the MPS EF-430 is a testament to efficiency and sustainability.
MPS